In der sich ständig weiterentwickelnden Elektroniklandschaft ist die Nachfrage nach innovativen und effizienten Lösungen von größter Bedeutung. Eine dieser Lösungen, die deutlich an Bedeutung gewonnen hat, ist die Rigid-Flex-PCB-Technologie. Dieser fortschrittliche Herstellungsprozess kombiniert das Beste aus starren und flexiblen Leiterplatten und bietet beispiellose Designflexibilität und Zuverlässigkeit. In diesem Artikel befassen wir uns mit dem Herstellungsprozess für starr-flexible Leiterplatten, den Vorteilen eines Komplettservices und der Bedeutung hochwertiger Prototyping- und Montagedienstleistungen.
Verständnis der Rigid-Flex-PCB-Technologie
Rigid-Flex-Leiterplatten sind Hybridleiterplatten, die starre und flexible Substrate in einer einzigen Einheit integrieren. Dieses einzigartige Design ermöglicht komplexe Schaltungslayouts bei gleichzeitig kompakter Form. Der Herstellungsprozess umfasst das Schichten flexibler und starrer Materialien, typischerweise Polyimid bzw. FR-4. Das Ergebnis ist eine vielseitige Leiterplatte, die sich ohne Leistungseinbußen biegen und biegen lässt.
Der Herstellungsprozess für starr-flexible Leiterplatten
Der Herstellungsprozess von Rigid-Flex-Leiterplatten ist kompliziert und erfordert Präzision in jeder Phase. Hier ist eine Aufschlüsselung der wichtigsten Schritte:
Design und Layout:Der Prozess beginnt mit einer detaillierten Designphase, in der Ingenieure mithilfe spezieller Software das PCB-Layout erstellen. Diese Phase ist entscheidend, da sie die Funktionalität und Leistung des Endprodukts bestimmt.
Materialauswahl:Die Auswahl der richtigen Materialien ist für die Herstellung hochwertiger Rigid-Flex-Leiterplatten von entscheidender Bedeutung. Die Kombination aus starren und flexiblen Substraten muss kompatibel sein, um Haltbarkeit und Leistung zu gewährleisten.
Schichtung:Im nächsten Schritt erfolgt die Schichtung der flexiblen und starren Materialien. Dies geschieht mithilfe fortschrittlicher Laminierungstechniken, die eine starke Verbindung zwischen den Schichten gewährleisten.
Ätzen und Bohren:Sobald die Schichten verbunden sind, werden die Schaltkreismuster auf die Oberfläche geätzt. Anschließend erfolgt das Bohren von Löchern für Durchkontaktierungen und die Platzierung der Komponenten.
Oberflächenveredelung:Der letzte Schritt im Herstellungsprozess ist die Oberflächenveredelung, die die Leistung und Langlebigkeit der Leiterplatte erhöht. Zu den gängigen Veredelungsoptionen gehören ENIG (Electroless Nickel Immersion Gold) und HASL (Hot Air Solder Leveling).
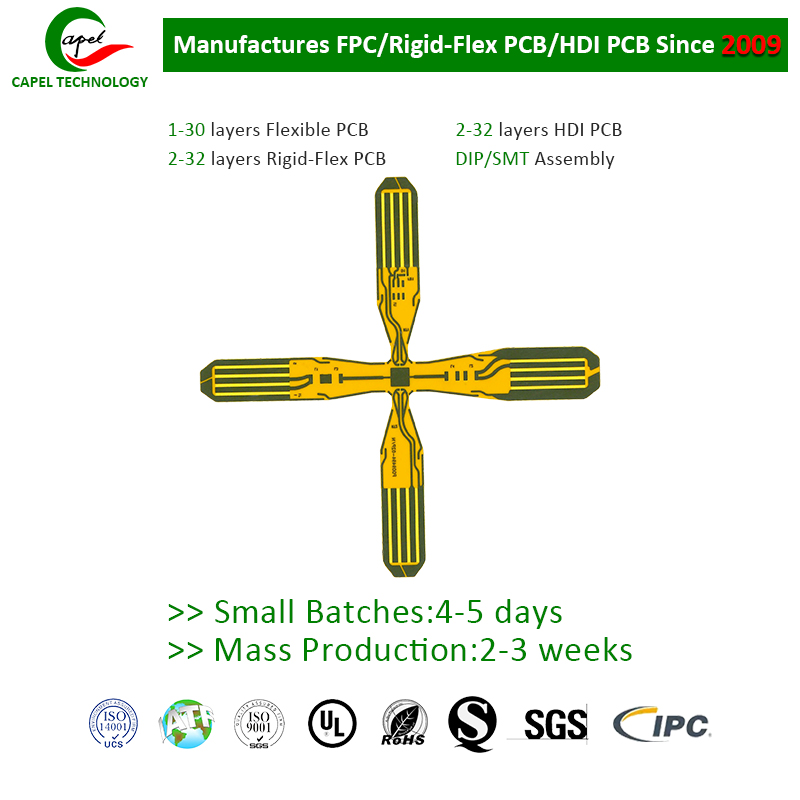
Die Bedeutung von Prototyping-Diensten
Die Prototypenerstellung ist eine kritische Phase im Herstellungsprozess von starr-flexiblen Leiterplatten. Es ermöglicht Designern und Ingenieuren, ihre Konzepte vor der Serienproduktion zu testen. Ein zuverlässiger Lieferant von starr-flexiblen Leiterplatten bietet umfassende Prototyping-Dienstleistungen an, die Folgendes umfassen:
Schnelles Prototyping:Um wettbewerbsfähig zu bleiben, sind kurze Bearbeitungszeiten unerlässlich. Ein Komplettanbieter kann Prototypen innerhalb weniger Tage liefern und so schnellere Iterationen und Designverbesserungen ermöglichen.
Testen und Validieren: Das Prototyping umfasst auch strenge Tests, um sicherzustellen, dass das Design alle Spezifikationen erfüllt. Dazu gehören elektrische Tests, thermische Analysen und mechanische Belastungstests.
Designänderungen:Basierend auf den Testergebnissen können Änderungen am Design vorgenommen werden. Dieser iterative Prozess ist entscheidend für die Erzielung eines qualitativ hochwertigen Endprodukts.
Montagedienstleistungen: Designs zum Leben erwecken
Sobald die Prototyping-Phase abgeschlossen ist, erfolgt der nächste Schritt mit der Montage. Um sicherzustellen, dass die Rigid-Flex-Leiterplatten wie vorgesehen funktionieren, sind qualitativ hochwertige Montagedienstleistungen von entscheidender Bedeutung. Ein Komplettanbieter bietet in der Regel folgende Montageleistungen an:
Komponentenbeschaffung: Ein zuverlässiger Lieferant verfügt über etablierte Beziehungen zu Komponentenherstellern, die den Zugang zu hochwertigen Teilen zu wettbewerbsfähigen Preisen gewährleisten.
Automatisierte Montage: Fortschrittliche Montagetechniken wie Pick-and-Place-Maschinen sorgen für Präzision und Effizienz im Montageprozess. Dadurch wird das Fehlerrisiko minimiert und die Gesamtqualität des Endprodukts verbessert.
Qualitätskontrolle:Strenge Qualitätskontrollmaßnahmen sind im Montageprozess unerlässlich. Dazu gehören visuelle Inspektionen, automatisierte optische Inspektionen (AOI) und Funktionstests, um sicherzustellen, dass jede Leiterplatte den erforderlichen Standards entspricht.
Die Vorteile eines One-Stop-Service
Die Wahl eines One-Stop-Dienstleisters für das Prototyping und die Montage starrer flexibler Leiterplatten bietet zahlreiche Vorteile:
Optimierte Kommunikation: Die Zusammenarbeit mit einem einzigen Lieferanten vereinfacht die Kommunikation und verringert das Risiko von Missverständnissen und Fehlern.
Kosteneffizienz:Ein One-Stop-Service kann aufgrund geringerer Gemeinkosten und des Großeinkaufs von Materialien oft zu besseren Preisen führen.
Schnellere Bearbeitungszeiten:Da alle Dienstleistungen unter einem Dach zusammengefasst sind, verkürzt sich die Zeit vom Design bis zur Produktion deutlich und ermöglicht so einen schnelleren Markteintritt.
Gleichbleibende Qualität:Es ist wahrscheinlicher, dass ein einzelner Lieferant in allen Phasen des Herstellungsprozesses, vom Prototyping bis zur Montage, eine gleichbleibende Qualität aufrechterhält.
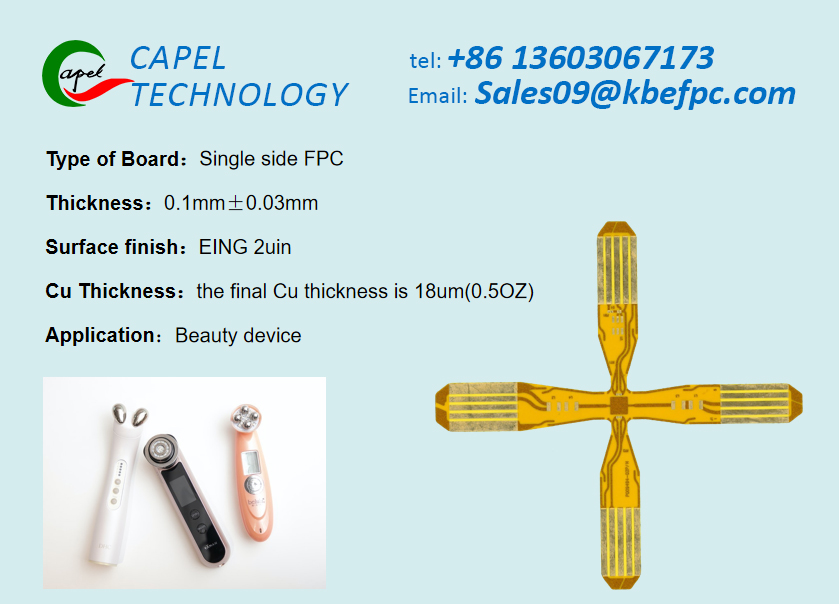
Zeitpunkt der Veröffentlichung: 22. Okt. 2024
Zurück